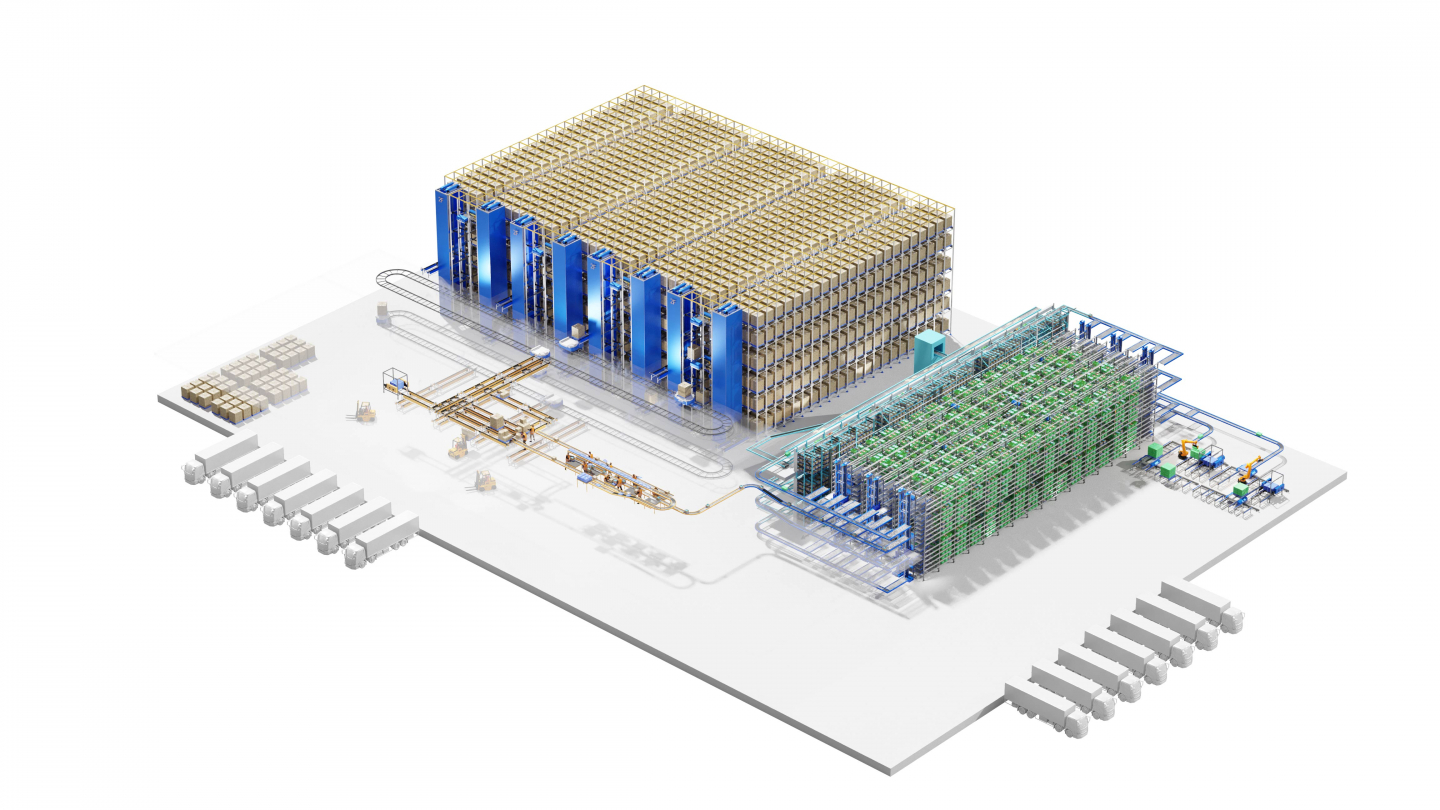
Order Fresh food online? Cold chain industry to seize low-temperature distribution opportunities
As the saying goes, food is of the utmost importance to the people, during the peak of the epidemic when the number of isolated people was surging, the demand for fresh and low-temperature food delivery exploded.
According to the statistics, among the 81,000 commercial trucks in Taiwan in 2020, about 9,680 trucks are carrying low-temperature goods, with an annual growth rate of 41.9%.
Enterprises' investment in low-temperature logistics has gradually developed from the single linkage of cold storage and cold transportation to the comprehensive cold chain logistics services such as cold chain park and low-temperature trunk transportation.
Taiwan's cold chain logistics industry is dominated by large 3PL low-temperature logistics B2B/B2C storage and transportation and 1PL group's self-built low-temperature logistics.
In this case study, we will introduce the B2B cold chain logistics storage solution, and get to know step by step how the multi-temperature vertical automatic warehouses, transportation, and picking operation works.
Why automation? Besides expanding storage space, efficiency and safety is also key factor.
Insufficient storage space for commodities
Frozen goods will have storage needs, unlike refrigerated foods which are mostly in over-the-top storage mode, and are mostly in large quantities with many items, so the demand for storage space in vertical pallet type is high.
Complicated goods are not easy to manage
The items are complicated and large, manually manage and non-vertical automation is not easy to control, which is time-consuming in operation.
Poor store picking efficiency
Traditional picking mode can not reach a variety of products at one time, picking efficiency is low, and under the “Goods-to-person” mode, staffs walking distance is long, the operation is complicated and time-consuming
Relying heavily on manpower
Sorting is the most labor-intensive and costly stage in logistics, and relying on a large amount of manpower makes productivity poor and difficult to break through.
Manual stacking aggravates the risk of personnel
The stacking operation of a large number of logistics boxes relies on manual operation, which is labor-intensive and increases the risk of occupational accidents and work injuries.
Difficult operation in cold environment
The efficiency of personnel working in low temperature environment is limited, and there is the limitation of operating time rotation in stages, and the risk of public safety is also higher than the general environment.
Purpose and estimated benefits
iAmech identified storage pain points in the fresh retail industry, we especially set the automatic equipment that can be imported at very low temperatures to achieve the purpose of vertical stocking, internal inbound/outbound data digitization, and operation process optimization.
The system can support various business models (such as B2B, B2C, O2O), minimize environmental impact through automatic load shifting, and seamlessly connect different temperature storage areas.
Also, the equipment is powered by supercapacitors, which can quickly adapt to the low-temperature environment, and finally, the storage materials are instantly configured.
We planned the intelligent automatic moving line to optimize the overall operational efficiency.
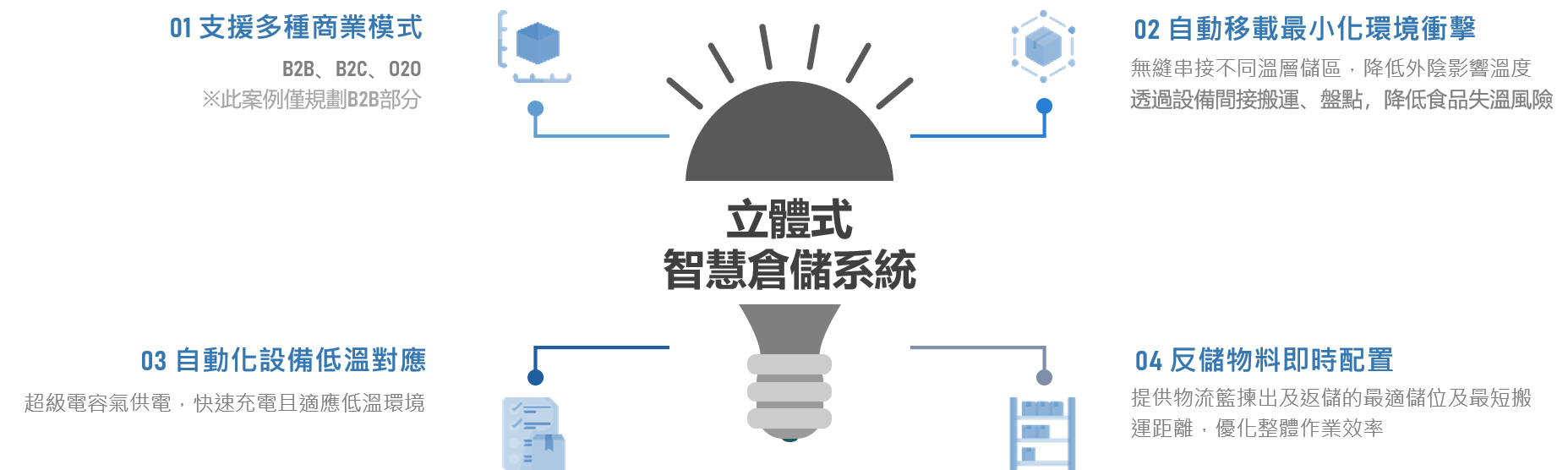
Solution
-
Seamless connection in restocking zone
-
Inbound/Outbound RGV Transport
The rail was laid in front of the inbound and outbound area, and the RGV (Rail Guided Vehicle) travels on a circular track, joining the automated warehouse behind to continuously support the inbound and outbound of goods, and the track makes transportation more efficient and stable.
-
High storage - Pallet Shuttle System
For the function of keeping stock, when the safety stock in the distribution warehouse is below the level, the pallet automatic warehouse will carry out replenishment, unstacking and box-cutting operations.
✔ Environment: -25℃
✔ Outbound capacity: 45 pallets/hr
✔ Excess material return capacity: 45 pallets/hrThe cartons/boxes travel to the replenishment operation area for cutting and loading, placing cartons on the unified carrier tray can make AS/RS more stable and improve picking efficiency.
-
Shuttle Rack System (SRS) – supporting temporary storage of picking and shipping
Tray containers are transferred back to the Shuttle Rack, and the two-way shuttle will carry them into AS/RS.
According to the system task instructions, the corresponding trays are transported to the side sowing sorting area for sorting, and the trays that are not yet shipped after sorting are returned to the complex SRS.
Therefore, SRS has the function of picking and temporary storage as well as temporary storage of outgoing goods, which supports efficient operation with short delivery time.
✔ Inbound capacity: 1800 boxes/hr
✔ Outbound replenishment and inbound picking capacity: 560 boxes/hr -
Sowing Sorting Zone with fluent shelf
The goods are transported to the fluent shelf through the vertical Miniload system, the sorting operation is carried out by personnel at the front, and then the goods are transported back to SRS after sorting.
The ambient temperature of the air curtain shutter is controlled at -25℃ between the fluent shelf and the picking area, and the whole operation takes no more than 30 minutes.
The final shipping stacking area is continuously stacked by robot arms, and the temperature is controlled in a freezing environment, and the SRS already follows the route when shipping, and pallets of the same area and route are stacked in the same area, making the distribution process more efficient and intelligently supporting the last mile of delivery.
The cold chain solution for retail B2B is not only a strong backup for low-temperature distribution in the market but also an all-around logistics center integrating upstream and downstream supply chains.
It can flexibly configure conveyor lanes and transportation equipment according to customers' needs, seamlessly linking picking and storage, transportation, sorting, and intelligent system evolution.
In the future, the demand for cold chain logistics and low-temperature distribution will grow faster when the technology of intelligent temperature measurement and control becomes more mature and the cost is reduced.
Deploy cold chain automation from now on to seize the new opportunity of supply chain.