SOLUTIONS
編輯器
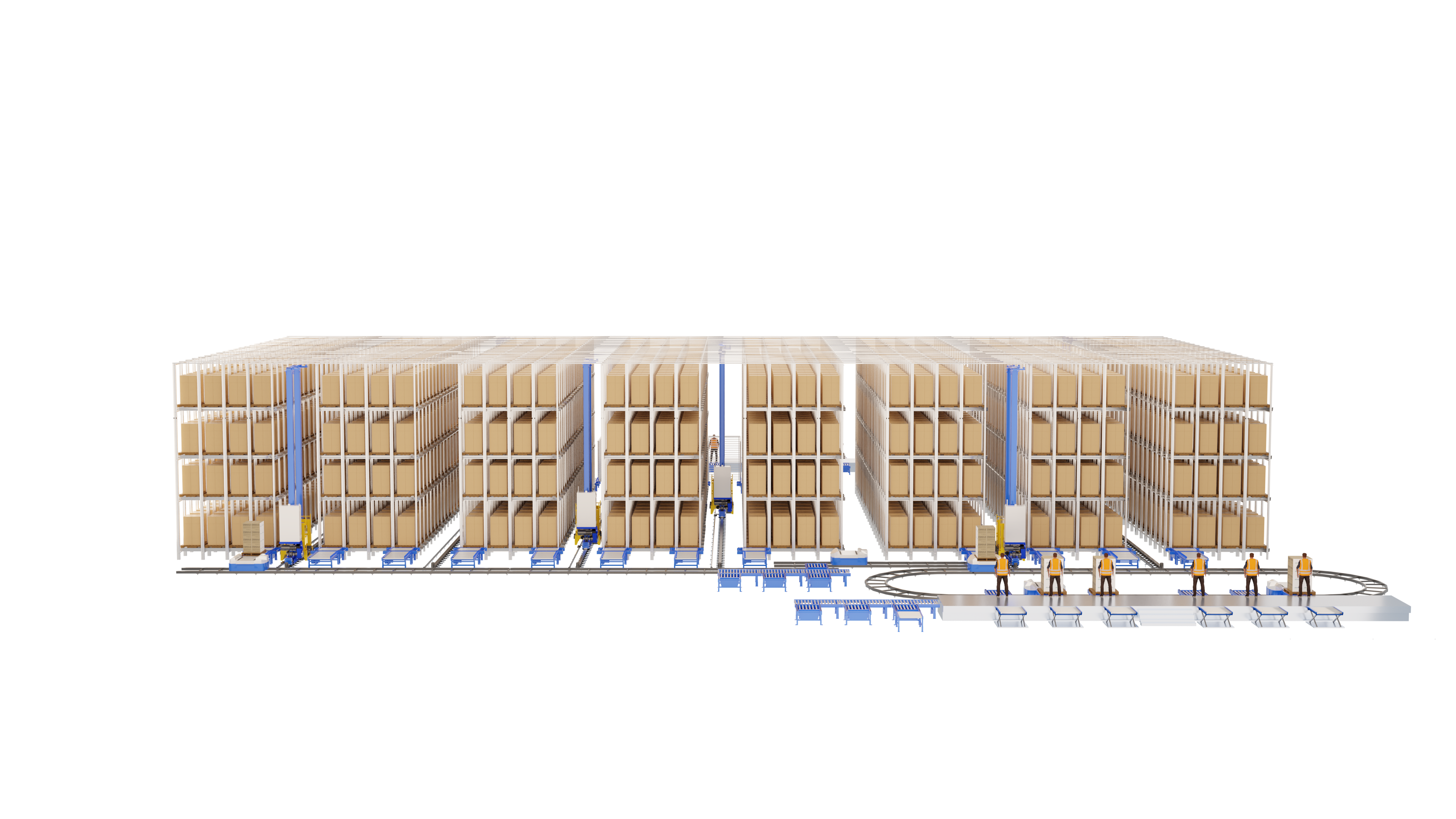
In this plan, iAmech provides solutions that can effectively increase the customer's competitive advantage in their industry. The Stacker Crane and Shuttle AS/RS is to handle a large number of storage needs through the integration of automated equipment and hardware and software and to achieve the purpose of “goods-to-person” by combining conveyor belts with Autonomous Mobile Systems.
It can not only improve the overall efficiency and optimize the operation process but also make significant improvements in labor shortage and space utilization.
● Advantages
- Goods-to-person mode reduces the public safety risk caused by the movement of people.
- Effective utilization of vertical and horizontal space in the factory with more storage space.
- Enhances product safety.
- Modular structure is suitable for flexible expansion.
- Reduces labor requirements in response to demographic changes.
- Automated system can pre-arrange the outbound process according to demand and move the pallets closer to the output area during the night, thus shortening the outbound time.
- WMS(Warehouse management system) can automatically generate operation reports, and the system analyzes various data to effectively control the performance.
- The user-friendly UI interface simplifies the training of operators and reduces time and cost.
● Operation Principles
- A/B/C Inventory management: Improving the outbound performance of large inventory
- Single-aisle, single-item storage strategy: improve outbound performance under FIFO strategy
- Dual storage area: Outbound transfer/ Flexible applications with multiple storage
● Process
編輯器
Inbound
Shipping side:
pallet positioning → (pallet wrapping) → automatic labeling → RGV loading → pallet stocking
Production side:
Pallet positioning → AGV loading → pallet stocking
Shipping side:
pallet positioning → (pallet wrapping) → automatic labeling → RGV loading → pallet stocking
Production side:
Pallet positioning → AGV loading → pallet stocking
Shipping side - Inbound operation
Step 1. Place the pallets on the inbound and outbound workstations by forklift, and label them automatically.
Step 2. The diverting conveyor automatically transfers goods on the conveyor and then proceeds to the inbound wrapping operation.
Step 3. RGV transfers the pallets to the inbound port.
Step 4. The pallet enters the inbound port.
Step 5. The pallets are stored in the storage space.
Production side - Inbound operation
Shipping side - Sorting operation
Step 2. The diverting conveyor automatically transfers goods on the conveyor and then proceeds to the inbound wrapping operation.
Step 3. RGV transfers the pallets to the inbound port.
Step 4. The pallet enters the inbound port.
Step 5. The pallets are stored in the storage space.
Production side - Inbound operation
Step 1. Place the pallets on the loading station by forklift.
Step 2. The system picks up the pallet from the pallet inlet loading station and turns to place it on the AGV.
Step 3. The AGV transfers the pallet to the inbound port.
Step 4. The pallet enters the inbound port.
Step 5. The pallet is stored in the storage space.
Step 2. The system picks up the pallet from the pallet inlet loading station and turns to place it on the AGV.
Step 3. The AGV transfers the pallet to the inbound port.
Step 4. The pallet enters the inbound port.
Step 5. The pallet is stored in the storage space.
Sorting
Shipping side:
Call the pallet→RGV loading→Pallet arrival→Sorting operation→(pallet wrapping)→Pallet back to warehouse
Production side:
Call the pallet→ AGV loading→ pallet arrival → picking operation → pallet return to warehouse
Shipping side:
Call the pallet→RGV loading→Pallet arrival→Sorting operation→(pallet wrapping)→Pallet back to warehouse
Production side:
Call the pallet→ AGV loading→ pallet arrival → picking operation → pallet return to warehouse
Shipping side - Sorting operation
Step 1. The system will move the pallets to the outbound port, and the RGV will move the pallets to the picking workstation.
Step 2. The staff picks the goods from the picking workstation and puts them on the pallets at the designated position.
Step 3. After the picking is completed, the RGV moves the pallets from the picking station back to the inbound port.If you need to re-wrap the pallet, it will be processed by the wrapping station first and then returned to the inbound port.
Step 4. The pallets are stored in the storage area.
Production side - Sorting operation
Step 2. The staff picks the goods from the picking workstation and puts them on the pallets at the designated position.
Step 3. After the picking is completed, the RGV moves the pallets from the picking station back to the inbound port.If you need to re-wrap the pallet, it will be processed by the wrapping station first and then returned to the inbound port.
Step 4. The pallets are stored in the storage area.
Production side - Sorting operation
Step 1. The system will discharge the pallets to the discharge port, and the AGV will transport the pallets to the picking workstation.
Step 2. The AGV transports the pallets to the picking workstation.
Step 3. The staff picks the goods from the picking workstation and puts them on the pallet on the lift.
Step 4. After the picking is finished, the AGV transports the pallets of the picking workstation back to the inbound port.
Step 5. Pallet goods is stored in the storage space.
Step 2. The AGV transports the pallets to the picking workstation.
Step 3. The staff picks the goods from the picking workstation and puts them on the pallet on the lift.
Step 4. After the picking is finished, the AGV transports the pallets of the picking workstation back to the inbound port.
Step 5. Pallet goods is stored in the storage space.
Shipment
Shipping side:
Call the pallet→RGV loading→Pallet arrival→Pallet out
Shipping side:
Call the pallet→RGV loading→Pallet arrival→Pallet out
Shipping side
Step 1. The system will ship the pallets to the outbound port.
Step 2. The RGV transports the pallets to the outbound workstation.
Step 3. The pallet steering machine automatically divert the pallets out.
Step 4. Pallet shipping out.
Step 2. The RGV transports the pallets to the outbound workstation.
Step 3. The pallet steering machine automatically divert the pallets out.
Step 4. Pallet shipping out.
編輯器
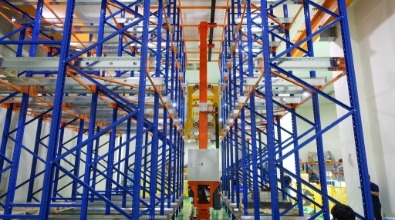
Stacker Crane and Shuttle AS/RS
✓ Flexibly adjustment of inbound/outbound process
✓ Effectively use of space
✓ Improve transportation efficiency
✓ connect AGV/RGV with conveyors
Conveyor AGV
✓ Rail-less to flexibly deploy
✓ Compact and high mobility
✓ Flexible bridging conveyors
✓ Support SLAM navigation and add QRCode precision positioning at conveyor interface
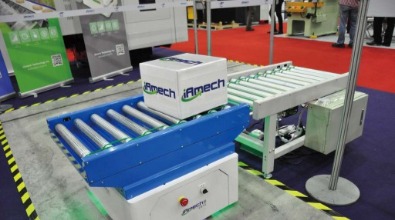
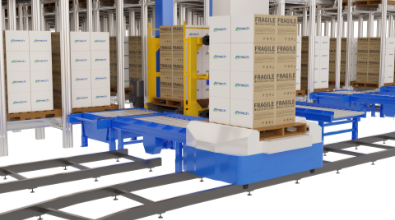
Rail Guided Vehicle(RGV)
✓ Track type design, fixed route, single action
✓ High-frequency operation and precise configuration
✓ Stable and efficient equipment
✓ Flexible bridging conveyors
編輯器
Benefit from the introduction of automation solution:
- Increase the number of pallets to 6114, making full use of vertical and horizontal space.
- Integration of software and hardware with SAP ERP system
- Effectively improve operation efficiency and transport speed to optimize throughput
6,144
Pallets
Storage space
66/33
In/Out per hour
Throughput
SAP/ERP
combined with SAP & ERP
Software
60
M/min
Handling speed